Chaire TwinHeat
The TwinHeat industrial chair proposes to use digital twins coupled with artificial intelligence to optimize existing furnaces, which are particularly energy-intensive and polluting.
This project, which originated at the Centre de Mise en Forme des Matériaux (CEMEF), aims not only to reduce energy consumption, but also to adapt processes to decarbonized energy sources such as electricity or hydrogen. It will enable the development of innovative solutions specific to industrial needs.
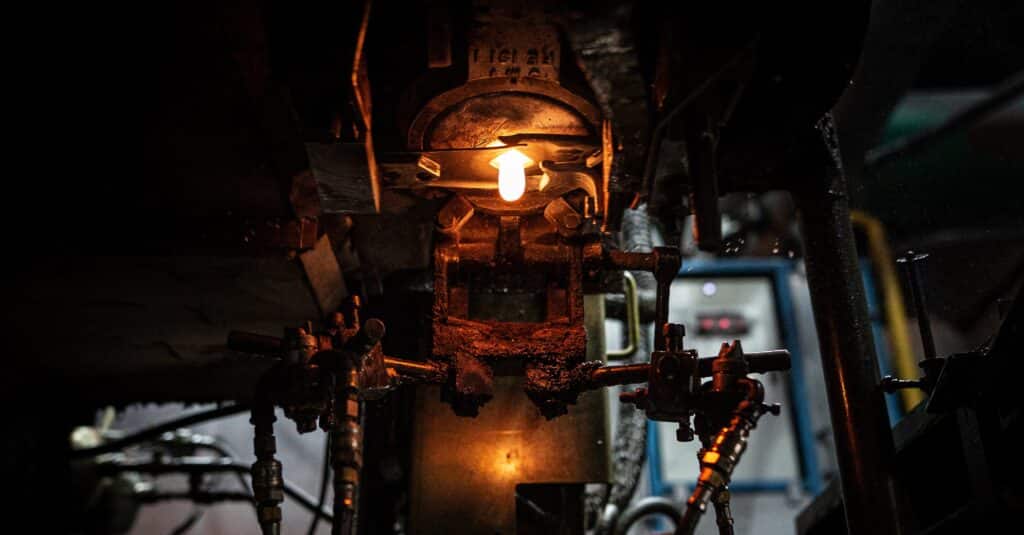
In the glass industry, furnaces are a widely adopted technology. In view of global climate change, advances are expected to reduce the CO2 footprint. This becomes all the more important as furnaces used to melt glass-forming liquid can reach temperatures of up to 1600°C: a process now considered one of the most energy-intensive and CO2-emitting in the world.
Numerical simulation is a standard tool for modeling furnaces. However, it remains complex and requires considerable computing time to accurately design a new furnace, limiting the number of cases tested and variants studied. This situation is further complicated by the ever-increasing number of operating cases and the need for flexibility in new industrial installations.
The Industrial Chair
The TwinHeat Industrial Chair provides a precise numerical framework for designing new furnaces and optimizing the control of existing ones. This framework makes it possible to improve the design of new heating systems aimed at reducing energy consumption or changing the energy source (decarbonated energy: electricity or hydrogen), to reduce the time and cost of furnace control (by reducing experimentation time), and to continuously develop safe and reliable products that meet customer specifications.
The innovative digital framework coupled with artificial intelligence is designed and implemented to:
- Optimize the operating conditions of existing furnaces,
- Study optimal combinations of heating parameters,
- Minimize energy consumption,
- Adapt to the energy transition, while respecting product quality constraints.
Two simultaneous actions are required to achieve this breakthrough:
- The development of a revolutionary machine learning-assisted numerical strategy for the accurate prediction of furnace fluid dynamics under well-defined and controlled conditions.
- The development of an integrated deep reinforcement learning strategy for the furnace control system, to be used as the basis for an automatic control and optimization system, including intelligent predictive models.
The industrial partners: four major national industrial groups facing these challenges will join forces to support the TwinHeat Chair, to create the digital twin of their own furnaces, to take advantage of its understanding, thermal behavior, control and finally optimization.
- Saint-Gobain
- Verallia
- Fives
- Pochet
- Sciences Computers Consultants (SCC)
The TwinHeat Chair thus contributes to a long-term vision of high-fidelity computational tools as a basis for reliable simulations of furnace processes, enabling partners to eliminate several major technical hurdles, support faster decision-making to supply high-quality materials, minimize energy consumption, avoid material rejection and thus optimize thermal processes.
Elie Hachem, Director of CEMEF
- Funding: One million euros from the French National Research Agency (ANR) and partners
- The Center: Centre de Mise en Forme des Matériaux (CEMEF)
- The coordinators: Elie Hachem, Director of CEMEF and Franck Pigeonneau, Lecturer at CEMEF