Digital twins for heat treatment, optimization and control of industrial furnaces: interview with Elie Hachem and Franck Pigeonneau, coordinators of the new TwinHeat industrial chair selected by the French National Research Agency (ANR)
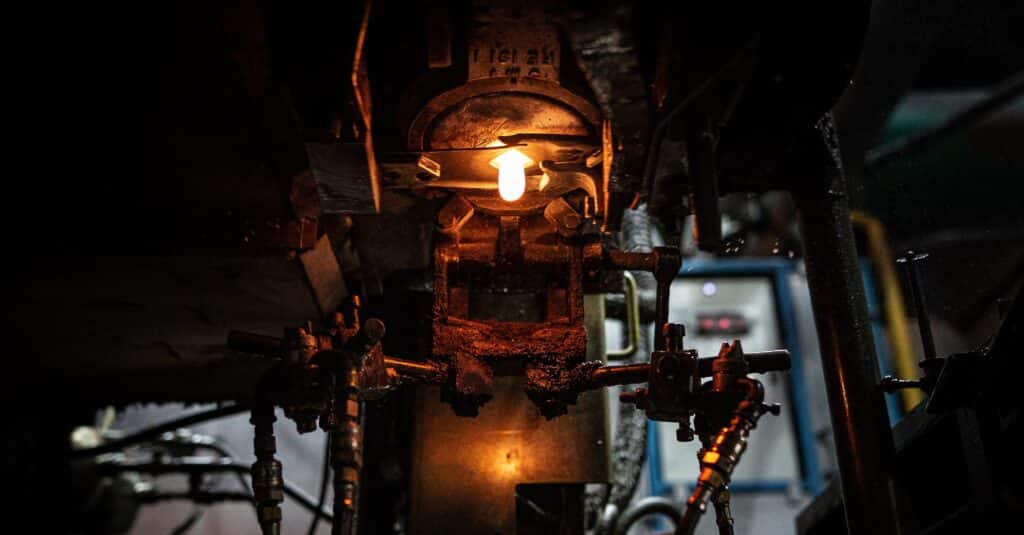
The glass industry, like many other sectors, faces major challenges in reducing its carbon footprint. The furnaces used to melt glass at extremely high temperatures are among the most energy-intensive and emit the most CO2. Numerical simulation is commonly used to model these furnaces, but it is complex and time-consuming, limiting the variants tested and the cases studied.
To address this problem, the TwinHeat industrial chair, recently funded by the French National Research Agency (ANR) to the tune of one million euros, proposes an innovative numerical framework coupled with artificial intelligence. The project aims to optimize the operating conditions of existing furnaces, study optimal combinations of heating parameters, minimize energy consumption and adapt to the energy transition towards decarbonized energy sources such as electricity or hydrogen. The project involves collaboration between four major industrial groups in the glass sector: Saint-Gobain, Verallia, Fives and Pochet, as well as SCC Sciences Computers Consultants.
Elie Hachem, Director of the Centre de Mise en Forme des Matériaux (CEMEF) and Franck Pigeonneau, Lecturer and Researcher at the Centre, coordinate this industrial chair. In this interview, they tell us about the motivations behind this project, the scientific challenges they plan to take up, and the technological innovations envisaged to transform industrial glass processes and reduce their carbon footprint.
Elie Hachem, Director of CEMEF
Franck Pigeonneau, Teacher-Researcher at CEMEF
Elie: “I’ve been developing the combination of digital mechanics and machine learning for several years now. This has naturally gone hand in hand with the introduction of digital twins, so much in demand in industry today. Combining innovation in this field with expertise in these subjects, I have succeeded in establishing our own specific definition of digital twins. You can’t call a product a digital twin without mentioning its utility. In effect, I’m proposing the digital twin of a process, enabling it to be optimized and controlled, thus meeting the needs of our industrial partners. In the case of this Chair, it will be the digital twin of the heat treatment process, capable of optimizing thermal installations (i.e. furnaces, feeders) and controlling them to meet each specification”.
Franck: “My research focuses mainly on the in-depth study of processes combining fluid mechanics, heat and mass transfer and inorganic chemistry. I try to mix both experimental and numerical approaches. Elie having developed both similar work of a more numerical nature but especially the use of learning methods enabled us to propose a project bringing together our two areas of expertise.”
Elie: “The implementation of a double artificial intelligence loop; the first for prediction coupled with digital furnace simulation, the second for optimization and control. It’s a new approach completely specific to the mines, combining expertise and innovation in the coupling of digital mechanics and machine learning.”
Franck: “On the technological front, breakthroughs are expected: is the transition from 100% electric furnaces producing flawless glass a conceivable reality? Having the digital twin of a furnace is also the challenge we want to meet.”
Franck and Elie: “The Chair plans to recruit 4 PhD students and two post-docs. We’ll start with two students in the first year and ramp up to full strength at the beginning of the second year of the Chair. The post-docs will come in the final year.”
Elie: “This chair fits in perfectly with the ANR’s call for industrial chair projects: to have an innovative part that responds to the most pressing needs of industrialists, but at the same time, one that is well mastered, as it is capable of providing real solutions to their needs at the end of the chair. In our case, it will be the digital twins of their installations and processes.”
Franck: “It’s hard to say until we have the ANR evaluation report. Based on last year’s report, the project addresses an important societal issue (reduction of carbon footprint and openness to Industry 4.0). Elie’s strategy at the audition was to respond to all the criticisms from last year.”
Franck: “The TwinHeat Chair aims to provide an innovative digital framework coupled with AI to improve the performance and reduce the carbon footprint of industrial furnaces, while guaranteeing the quality of finished products. By numerical framework, we mean the numerical simulation of flows and heat transfers in furnaces.”
Elie: “By innovative digital framework, we mean the coupling of digital mechanics and machine learning for the development of a digital twin specific to the optimization and control of heat treatment processes.”
Franck: “Glass producers (Saint-Gobain, Verallia, Pochet) and others are committed to reducing their carbon footprint, with a zero-carbon target for 2050. To achieve this, they need to rethink the way their products are made. One way is to change the source of the energy needed to produce glass (electricity, H2, bio-gas, etc.). For them, the Chair is an opportunity to explore new heating methods and optimize existing ones. For furnace designer Fives, the aim is to equip itself with expert systems for controlling the operation of industrial facilities. The development of the digital twin applied to furnaces is a major asset for them.”
Elie: “Our expertise in coupling digital mechanics and artificial intelligence has enabled us to understand that the usefulness of a digital twin depends above all on its purpose. Indeed, we take advantage of the power of the latest algorithms in deep learning, either to predict or to make decisions to intelligently optimize a system, to control a situation or to test scenarios, hypotheses and help make decisions.”
Elie: ” SCC specializes in the development of industry-specific software, in particular for the simulation of industrial furnaces. On the one hand, the addition of artificial intelligence to its offer is essential these days, and on the other, benefiting from its expertise to extend and disseminate the digital twin solution resulting from this Chair, will increase the impact and visibility of our research.”
Elie: “Indeed, Mines Paris – PSL are well known, particularly through CEMEF, as world experts in digital solutions for forming. Our strategy is to pursue and couple this expertise with artificial intelligence. Fully aware of the complexity of simulating industrial processes, we have designed a double artificial intelligence loop; the first for “learning for prediction” coupled with digital simulation of furnaces, the second for “learning for optimization and control” completely specific to our partners for decision-making assistance meeting their specifications: product quality and environmental impact.”
In the glass industry, furnaces are a widely adopted technology. In view of global climate change, advances are expected in reducing the CO2 footprint. This becomes all the more important as furnaces used to melt glass-forming liquid can reach temperatures of up to 1600°C: a process now considered one of the most energy-intensive and CO2-emitting in the world.
Numerical simulation is a standard tool for modeling furnaces. However, it remains complex and requires considerable computing time to accurately design a new furnace, limiting the number of cases tested and variants studied. This situation is further complicated by the ever-increasing number of operating cases and the need for flexibility in new industrial plants.
A precise numerical framework for designing new furnaces and optimizing the control of existing ones is a subject of major importance. It enables us to improve the design of new heating systems aimed at reducing energy consumption or changing the energy source (decarbonized energy: electricity or hydrogen), to reduce the time and cost of furnace control (by reducing experimentation time), and to continually develop safe and reliable products that meet customer specifications.
Despite industry’s obvious interest in accurate modeling and control of heating processes, there is no comprehensive study or general answer to this problem in an industrial context. An innovative numerical framework coupled with artificial intelligence needs to be designed and implemented to:
Two simultaneous actions are required to achieve this breakthrough: firstly, the development of a revolutionary machine learning-assisted numerical strategy for the accurate prediction of furnace fluid dynamics under well-defined and controlled conditions. Secondly, the development of an integrated deep reinforcement learning strategy for the furnace control system, to be used as the basis for an automatic control and optimization system, including intelligent predictive models.
Four major national industrial groups facing these challenges will join forces to support the TwinHeat Chair, to create the digital twin of their own furnaces, to take advantage of its understanding, thermal behavior, control and finally optimization: Saint-Gobain, Verallia, Fives and Pochet. Following the recommendation of the chair panel in 2023, a new partner will strengthen the consortium’s ability to disseminate this digital twin technology and exploit its full potential at industrial level: SCC Sciences Computers Consultants, with 30 years’ experience in the development and marketing of digital simulation software dedicated to industrial materials transformation processes.
The TwinHeat Chair thus contributes to a long-term vision of high-fidelity computational tools as the basis for reliable simulations of furnace processes, enabling partners to eliminate several major technical hurdles, support faster decision-making to supply high-quality materials, minimize energy consumption, avoid material rejection and thus optimize thermal processes.
For the 6th time, CEMEF is awarded an ANR grant. One of the ANR’s missions is to stimulate cooperation between public and private research players, as reflected in the “Chaires Industrielles” program dedicated to partnership research, which is part of the “Economic impact of research and competitiveness” component of the ANR’s Action Plan.
Mines Paris – PSL trains tomorrow’s engineers in sustainable practices, notably through the design of concentrated solar furnaces, in collaboration wi...