On January 16, 2024, Edouard de Sonis, a doctoral student at the Centre des Matériaux de Mines Paris – PSL, defended his doctoral thesis on the “Étude des relations microstructure – comportement à rupture d’aciers 316L élaborés par procédés LPBF et WAAM” (“Study of microstructure – fracture behavior of 316L steels produced by LPBF and WAAM processes”). These two additive manufacturing processes, LPBF (Laser Powder Bed Fusion) and WAAM (Wire Arc Additive Manufacturing), represent major advances in metallurgy and industrial manufacturing. Edouard de Sonis’ work explores in depth how the microstructure of 316L steels, modified by these processes, influences their mechanical behavior, and in particular their fracture resistance.
Edouard de Sonis was awarded the 2nd Prix BODYCOTE 2024 by the SF2M at the Journées Annuelles de la SF2M ceremony held on November 18, 2024 at the CNAM-Paris. The prize recognizes the originality and impact of this research, which could have significant repercussions on industry, particularly in the decarbonized energy sector, where 316L steels are widely used for their mechanical and corrosion-resistant properties. The target application? Securing the (re)fabrication of parts for the life extension of existing nuclear power plants, and the corresponding certification methodologies.
This award highlights the growing importance of additive manufacturing processes in the development of materials with optimized mechanical properties and dimensioning methodologies adapted to these new metallurgies.
3 questions to Edouard de Sonis:
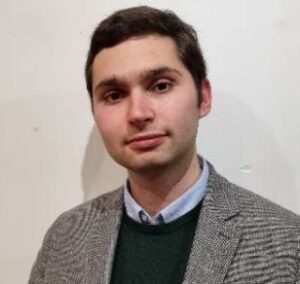
What prompted you to choose 316L steels and the LPBF and WAAM processes for your research?
The aim of the research project to which my thesis belonged was to study the influence of additive manufacturing processes on the microstructure and mechanical behavior of some of the materials used in nuclear reactors currently in service. Among these materials, 316L steel is widely used for many small components (valve bodies, filters, etc.).
With regard to the two processes studied, the interest lay in their difference in scale, both in terms of the microstructures obtained and the parts manufactured. The LPBF process is generally used to manufacture parts measuring just a few centimetres, whereas the WAAM process can be used to manufacture parts measuring several metres. Similarly, the characteristic sizes of microstructures obtained by WAAM are (at least for 316L steel) around an order of magnitude larger than those obtained by LPBF. Other metal additive manufacturing processes (DED, WLAM, etc.) are at intermediate scales. The combined study of these two “extreme” processes has therefore enabled us to sketch out a global vision of the microstructures of 316L steel that can be obtained by additive manufacturing, and of their fracture behavior.
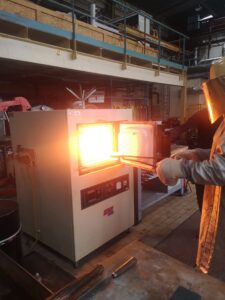
Illustration of heat treatments performed on LPBF and WAAM 316L steel
What were the main technical challenges encountered in your work on the relationship between steel microstructure and fracture?
One of the main technical challenges was to obtain porosity-free materials, which can only be achieved by optimizing and controlling manufacturing parameters.
Another challenge concerned the normative aspect of mechanical testing, particularly crack propagation testing. It became apparent that the results obtained could vary significantly depending on the test standard used (ISO or ASTM). It was therefore necessary to reflect on the use of these standards in order to determine which applied best to the materials studied.
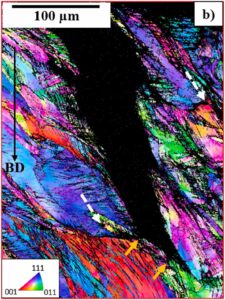
A propagating crack in 316L LPBF steel
How could your results influence the industrial applications of 316L steels in the years to come?
My thesis work has enabled us to gain a better understanding of the fracture behavior of 316L steel produced by the LPBF and WAAM processes. In addition, it has been shown that, while these materials have a lower resistance to crack propagation than forged 316L steel, the criteria of the standards imposed by the nuclear industry have been met in the majority of microstructural cases studied. This paves the way for the qualification and potential use of 316L steel parts developed by LPBF and WAAM in operating reactors.