Interview with Maryse Gille: 2nd prize for best presentation at the 19th European Mechanics of Materials Conference EMMC19
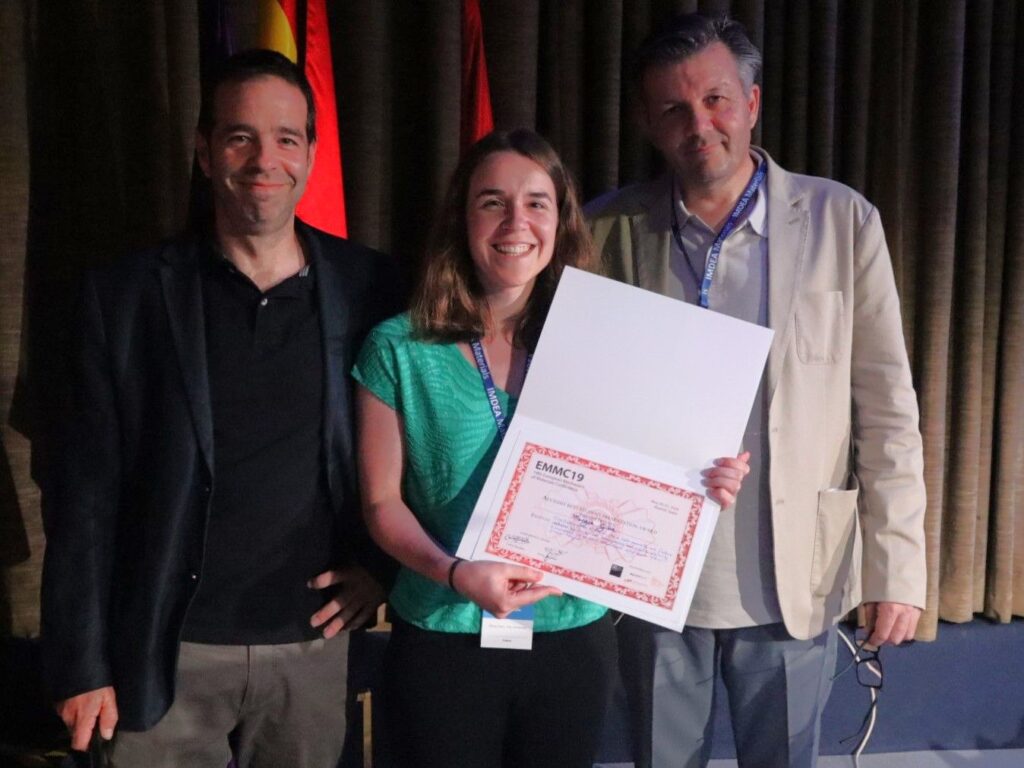
Using innovative digital simulation techniques and tomography, a 3D imaging technique widely used in the mechanics of materials, but also in medical imaging and geophysics, Maryse Gille explores the deformation heterogeneities leading to fracture of these materials, which are essential to the automotive industry. Her work promises to optimize the formability of aluminum alloys which, by replacing steel, help reduce CO2 emissions.
In metals such as aluminum, the material is arranged in the form of grains several tens of microns in size, and the aim of my work is to study the effect of these grains on the deformation heterogeneities leading to sheet failure during forming.
Maryse Gille
Figure illustrating the methodology employed in the thesis: acquisition of 3D scans of the specimen by tomography and processing of these scans by finite element simulation and image correlation to then compare the two results.
“In my thesis, I’m interested in an aluminum alloy used for car bodies. One of the criteria to be met is that the sheet must be able to deform sufficiently without breaking to achieve the desired geometry. However, the material doesn’t deform homogeneously, and a heterogeneous deformation field can be observed very early on. In concrete terms, bands of more intense deformation are formed, and these persist until fracture occurs at that point. In metals such as aluminum, the material is arranged in the form of grains several tens of microns in size, and the aim of my work is to study the effect of these grains on the deformation heterogeneities leading to sheet failure during forming.”
“The advantage of X-ray tomography is that – as is the case in medicine – we can non-destructively obtain a three-dimensional image of a volume. This is of real interest, as it enables us to study the same 3D volume over time.
The first technique used here – called diffraction contrast tomography (DCT) – provides a three-dimensional mapping of the grains present in my initial specimen, whereas the usual technique – called EBSD – only allows grains to be imaged on a 2D surface.
The second technique I use is in situ absorption tomography. I acquire several scans of the same specimen as it deforms until it breaks. By following the contrast within the deforming material, I can measure local deformations (image correlation technique using the contrast created by the presence of intermetallic particles). It’s common practice to measure deformations on the surface of a specimen by applying a paint speckle, but using the material’s “natural speckle” allows me to measure inside the material.”
“As I explained earlier, X-ray tomography allows me to access different information in the 3D volume of the specimen:
The digital twin of the specimen allows me to carry out simulations that take account of the microstructure measured non-destructively on the undeformed specimen (3D element-finite simulations of crystalline plasticity). The aim is therefore to carry out calculations at large deformations and compare the results obtained with experimental measurements made on in situ absorption tomography scans.”
“First of all, we observed early heterogeneity of the deformation field in the alloy studied. This heterogeneity takes the form of spatially stable bands, which appear where the final fracture occurs. Then, using the digital twin of the test specimen, we found that the simulated results corresponded well to the measurements made during actual deformation tests. This shows that the material’s grains play an important role in the observed deformation heterogeneity, and that our simulations are useful for understanding how these grains influence material fracture.”
“From an experimental point of view, the main difficulty was dealing with an unexpected misalignment between diffraction and absorption contrast tomography scans. This misalignment made direct comparison between image data and material deformation simulations impossible. What’s more, when working with 3D data on samples with symmetries, it’s crucial to properly manage local rotations and landmarks, which can vary from one piece of data to another. To solve these problems, I spent several months of my thesis carefully aligning the data from the broken sample.
On the numerical side, the challenges were mainly related to creating an appropriate mesh of the microstructure, which was not too refined to avoid long computation times. For this, I enlisted the help of Romain Quey, a researcher at Mines de Saint-Etienne, who developed the Neper software, which enabled me to overcome these obstacles.”
“My research has shown the relevance of using crystalline plasticity simulations to study the role of grains on deformation heterogeneities leading to fracture of an aluminum sheet during forming. With this understanding of the mechanisms involved, manufacturers could adapt the microstructure of aluminum alloys accordingly to optimize their formability.”
“I’m currently finalizing the writing of an article to publish these results. I also still have a few experimental analyses to carry out, such as image correlation on an in situ nano-tomography experiment which is very similar to the one I’ve described here but with more resolved scans. Finally, as I’m nearing the end of my thesis, I’m going to concentrate on writing my manuscript in order to submit it on time.”
Maryse Gille at the award ceremony for best presentation at EMMC19