The Cold Spray revolution: the art of dynamic spraying redefines the manufacture and repair of metal parts
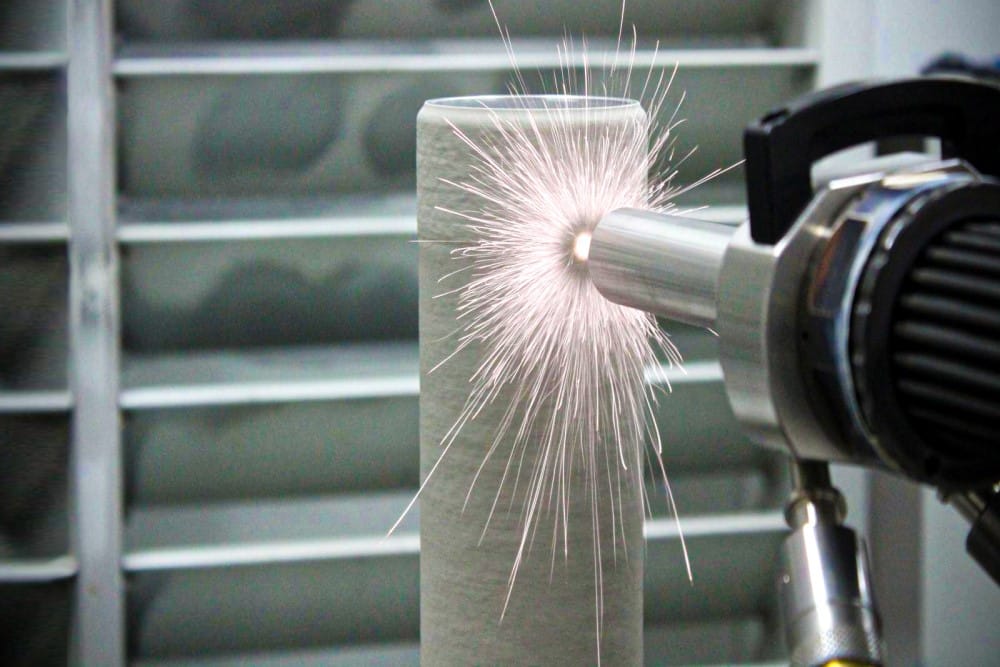
The Cold Spray process is based on the acceleration of powder particles, sprayed by a heated, pressurized gas, to supersonic velocities through a convergent-divergent nozzle. In the first, convergent part of the nozzle, the flow is brought up to the speed of sound, while in the second, divergent part, the flow is accelerated to supersonic speed by an expansion process similar to that used in rocket engines. The particles, which have acquired high velocities while maintaining a relatively low temperature, are projected in a solid state onto a substrate. Their plastic deformation on impact activates certain mechanisms – still debated in the scientific community – responsible for their adhesion to the substrate.
Diagram showing the evolution of pressure (P), velocity (V) and temperature (T) along the sections of a convergent-divergent nozzle. Temperature and pressure drop as the gas progresses, while its velocity increases until it reaches the speed of sound at the throat.
It is thus possible to build a material deposit by stacking deformed powder particles on the substrate, opening up a wide range of applications. These can be grouped into three main categories:
Cold sprayed metal-metal composite coating. The substrate appears in black in the lower part of the image. The matrix is stainless steel and the lighter particles are made of tool steel (very hard). The black areas in the coating are pores. From Laurent Aubanel’s thesis.
Although increasingly recognized, this cold deposition technique is still considered innovative. The cold spray process has enjoyed undeniable growth in recent years, as it offers the possibility of producing dense, thick metal deposits while maintaining the purity of the sprayed powders. These sought-after characteristics, combined with the availability of robust industrial equipment that can be integrated into a production line, continue to generate keen interest in many industrial sectors such as aeronautics, biomedical and energy.
The Centre des Matériaux Pierre-Marie Fourt at Mines Paris – PSL was one of the first laboratories in France to install a cold spray system, in the early 2000s. Michel Jeandin, the laboratory’s research director at the time, made a major contribution to the development of the process in France, thanks to numerous studies. Vincent Guipont and Francesco Delloro, two teacher-researchers at the Center, continued and developed the activity following Michel Jeandin’s retirement.
Michel Jeandin, Director of Research at the Centre des Matériaux de Mines Paris – PSL, gives his inaugural presentation at the THERMEC’18 international conference at the Cité des sciences et de l’industrie in Paris.
The cold spray research activity at the Centre des Matériaux includes numerous projects, some in collaboration with industry. Over the past four years, seven doctoral theses on this process have been supervised and defended within the laboratory. For example, Laury-Hann Brassart’s thesis (defended in 2022), financed by EDF, studied the properties of a stainless steel manufactured by cold spray and their evolution when heat treatment is applied to improve mechanical performance.
Bending tests on thick stainless steel coatings on steel, obtained by cold spray. Without heat treatment, cold spray material is rather brittle. Heat treatment restores good ductility. Based on L.-H. Brassart’s thesis, in collaboration with EDF.
The research carried out on cold spray is undeniably recognized for its high quality, as demonstrated by the prizes awarded in 2023. Laurent Aubanel was awarded the SF2M Bodycote prize, as well as the Hirn prize for the best French thesis in tribology (the science of wear, friction and lubrication) for his thesis entitled “Etude du comportement tribologique en régime lubrifié de revêtments cold spray composites à base d’acier”, carried out at the Centre des Matériaux, in partnership with Renault and defended in 2022. In addition, Michel Jeandin was inducted into the Thermal Spray Society’s Hall of Fame and awarded the IHHTSE – International Federation for Heat Treatment and Surface Engineering – Medal for lifetime achievement in Yokohama.
Laurent Aubanel, spécialiste des matériaux et des revêtements, ainsi que de leurs procédés de mise en œuvre, auteur d’une thèse intitulée “Étude du comportement tribologique en régime lubrifié de revêtements cold spray composites à base d’acier”, réalisée au Centre des Matériaux, en partenariat avec Renault.
The use of laser shock is proving to be a remarkable tool in the study of cold spray. This technique is based on the use of a laser that emits very short pulses (a few nanoseconds), enabling high power to be concentrated in a very short time. The interaction of this laser with the material generates an intense mechanical compression wave (the shock), which propagates through the material. Two laser shock developments applied to materials produced by powder spraying to obtain coatings (cold spray, plasma, flame, etc.) have been initiated at the Materials Center: the LASAT (Laser Shock Adhesion Test) and the LASHPOL (Laser Shock Powder Launcher). Currently, laser shock equipment is being used to develop the LSD (Laser Shock Densification) process for porous components.
The Centre des Matériaux is also committed to sharing knowledge and networking cold spray players, through the creation in 2006 and leadership of the Club Cold Spray; the Club aims to bring together laboratories, transfer centers and industrial companies interested in the cold spray process. Over the years, the Club has grown to become the leading European event for this process. The Club’s mission is to present and discuss issues relating to the understanding of cold spray and the analysis of materials produced by this new process. To this end, the Club proposes active exchanges based on presentations and panel discussions at meetings, and promotes networking between academic and industrial members from all over the world.
Find out more about the Cold Spray Club
There are still a number of obstacles to be overcome, justifying the need for further research in this field.
In particular, the issue of powder remains central to the performance of cold spray materials. While some materials, such as most pure metals, can be sprayed fairly easily, many alloys of industrial interest have difficulty being used in cold spray, which is a considerable brake on the emergence of new applications. The solution to these problems often lies in powder. The studies and methods developed at the Centre des Matériaux help us to understand whether the reasons for a material’s poor sprayability are actually to be found in the powder and, if so, can also provide relevant solutions, through the selection or modification of powders.
Transposing the process to the production of ceramic deposits involves knowing how to make powders of a brittle material, thrown at high speed, adhere to a substrate, bouncing it as little as possible and avoiding “stripping” the substrate with the powder. As part of the ANR CERASOL project (2019-2023) coordinated by V. Guipont, in collaboration with IRCER in Limoges and two French manufacturers of ceramic powders (Nanoé and Medicoat France), Geoffrey Céleste’s thesis (defended in 2023) has advanced knowledge of the construction of ceramic deposits by cold spray, based on architecturally-designed powders designed to dissipate impact energy favorably, as well as on the development of the low-pressure cold spray process under vacuum (EPROM platform at the Centre des Matériaux). Thanks to the laboratory’s mastery of several additive manufacturing processes, it is possible to interface these processes to create junctions between materials. For example, a first thick coating is deposited “cold” by cold spray on a substrate that would be incompatible in the presence of a dilution zone resulting from melting (formation of brittle intermetallics). Then, on this first layer, it becomes possible to build by laser fusion using a metal 3D printer. The foundations for this interlinking of processes were laid with a nickel-based superalloy in Cléa Plouze’s thesis (defended in 2022).
About Francesco Delloro
Francesco Delloro, teacher-researcher at the Centre des Matériaux, specializes in thermal spray processes, in particular cold spray. Author of a thesis entitled “Combined morphological and finite element methods for a new approach to 3D modeling of cold spray deposition”.
About Vincent Guipon
Vincent Guipont, PhD from Ecole Centrale de Lyon in 1994, joined the Materials Center in 1996. He obtained his HDR from the University of Limoges in 2013. An expert in the field of materials, surfaces and interfaces, focusing mainly on thick coatings obtained by plasma spraying and cold spray, he has developed a theme in the field of laser shock treatment and played an active part in the development of LASAT and its extensions in the mechanical characterization of substrate-coating interfaces. He is currently co-developing the LASDAM methodology for studying the lifetime of thermal barriers.
In 2023, the Centre des Matériaux (CMAT) at Mines Paris – PSL received a number of prestigious awards, testifying to the excellence of its researchers...