Interview with Marc Bernacki, winner of the Albert Portevin 2024 medal: recognition for 20 years of research in computational metallurgy
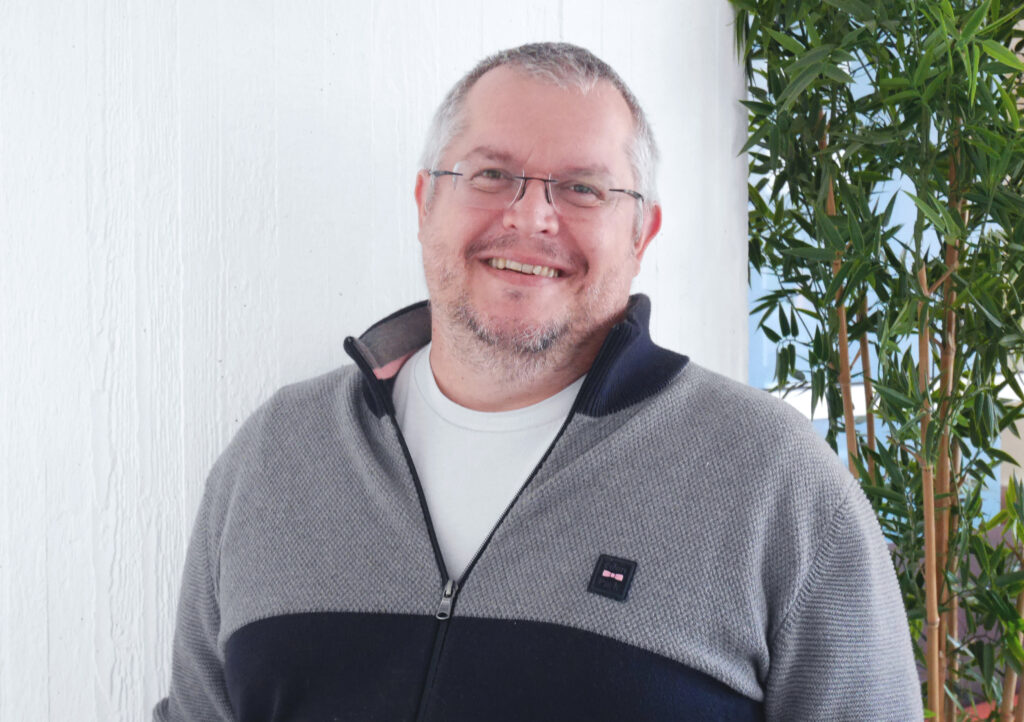
On November 18, 2024, Marc Bernacki will be honored with the Albert Portevin Medal, an award celebrating his contributions to physical and computational metallurgy. The prize, awarded by the Société Française de Métallurgie et de Matériaux (SF2M), crowns twenty years of innovative research in the field of high-performance computing applied to metallic materials.
Marc Bernacki, professor at Mines Paris – PSL and head of the MSR team at CEMEF, contributes through his research to the development of multi-scale numerical methods for describing and predicting the complex microstructural transformations that occur during metal forming processes. His work follows in the footsteps of Albert Portevin (1880-1962), whose research into metallic materials continues to have a major impact on strategic sectors such as aerospace, defense, energy and transport.
Marc Bernacki’s presentation at the Albert Portevin 2024 medal ceremony on November 18.
Over the past 20 years, Marc Bernacki has succeeded in combining fundamental science with industrial applications. By creating original numerical tools to model polycrystalline materials, his team has gained a better understanding of microstructural phenomena such as macle formation, grain boundary evolution and the mobility of crystalline defects. These topics are key to optimizing metallurgical manufacturing processes and materials, and are supported by constant collaboration with experts in experimental metallurgy. It’s important to remember that the stakes are high from an environmental point of view (better respect for resources, less waste during production and energy optimization), from a societal point of view (safer materials) and also in terms of national sovereignty for the design of more efficient materials and processes in high-stake areas such as energy, aeronautics and space.
Numerical reconstruction of a polycrystalline microstructure of an aeronautical alloy (Inconel718) with exact description of second-phase particles and grain boundary statistics.
Marc’s two ANR industrial chairs and his leadership of the Digimu consortium illustrate his dynamism and his role as a link between fundamental research and concrete applications. The simulations he has developed are now also being applied to emerging fields such as powder metallurgy, non-destructive testing and research into geological and extraterrestrial materials.
Photo of the DIGIMU 2024 consortium at Framatome – RealMotion Chair.
Photo of several PhD students and permanent staff from the DIGIMU consortium at SafranTech in 2018.
In addition to his academic contributions, Marc attaches great importance to passing on his knowledge. He has trained several generations of young researchers by supervising theses, post-doctorates and teaching at Mines Paris – PSL. His commitment to partnerships with industry also demonstrates his determination to meet the concrete needs of major industrial sectors.
To mark the award of the Albert Portevin Medal, Marc Bernacki looks back on his career and shares his thoughts on the prospects for computational metallurgy and his personal career at the École.
The physical metallurgy at work in hot forming has been a subject of study for 120 years, and the major theories that led to the first phenomenological models (still often used today in academia and industry) date back to the middle of the twentieth century. Nonetheless, today we realize that physical and experimental metallurgy are still very much alive and kicking in terms of academic research, as many phenomena/mechanisms are still misunderstood or are being discovered in connection with increasingly complex compositions and processing methods. For example, until about twenty years ago, there were no truly predictive simulation tools for the evolution of polycrystalline metallic materials during their development, which is a crucial need in this field. While some numerical developments have been arduous in their elaboration and in the minimization of their numerical cost, the most difficult task has probably always been to confront the reality of real ranges, materials and industrial issues.
High-strain modeling of a polycrystalline material (austenitic steel, nuclear grade) with crystal plasticity calculations for the prediction of crystallographic orientations and dislocation densities.
In fact, our team interacts with many top-level foreign teams on so-called academic simulations, i.e. where we need to validate our simulation tools on ideal conditions, and materials that are just as ideal, to predict certain specific mechanisms at equilibrium. In this field, we have developed a number of original numerical methods that enable us to propose differentiating and generic approaches. However, our main achievement probably lies in the fact that we have gone beyond pure materials and ideal conditions. In fact, the reality of industrial processes is quite different: the mechanisms are multiple, the microstructures always out of equilibrium, the materials of unparalleled complexity, and it is in this field that we have achieved major breakthroughs, helping to understand certain mechanisms, and enabling the optimization of industrial ranges. Very few teams dare to venture into these areas. Moreover, it is these successes that enable us to meet the major environmental, societal and sovereignty challenges detailed above.
General research theme of the MSR team.
IF from an academic point of view, it’s quite easy to answer this question through publications and methods that are then reused and improved in the community; from an industrial point of view it can be much more difficult to answer in such a precise way. Indeed, where the success of a truly predictive numerical method validated with our industrial partners ends, the industrial confidentiality of the successes that may result in the field often begins. Nevertheless, it’s gratifying when we hear, in passing, that such and such a simulation has made it possible to significantly reduce the rate of rejects in the manufacture of a part, or when patents for inventions developed on the basis of numerical test campaigns carried out with our tools can be filed to prevent the appearance of critical defects in strategic parts.
The backbone of our team has always been a physical and experimental understanding of the phenomena we are trying to model. It’s difficult, but it gives us a generic view of the physical mechanisms at work and enables us to apply our know-how to different materials. For example, some of the mechanisms at work in polycrystalline metallic materials, in order to predict their mechanical properties, can be extended, with a different scale of time and space, to rocks to provide hypotheses on their geological history. Pushing to the extreme the analogy between the fine characteristics of the resulting microstructures and the potential underlying “thermomechanical” history/events, we are also fortunate to be able to collaborate on projects involving extraterrestrial materials from asteroids, with colleagues from the Observatoire de la Côte d’Azur, the University of Arizona and NASA.
Numerical representation of an asteroid regolith to model its thermal response to sunlight
This generic approach to mechanisms and numerical methods also enables us to be highly agile when it comes to new processes. For example, we have a number of developments dedicated to powder metallurgy and additive manufacturing, for which the need for numerical twins is paramount.
Numerical representation of a dense polydisperse aggregate of powder particles with application to powder metallurgy.
Improvements in non-destructive testing techniques and their modeling within heterogeneous materials also point to the future of non-destructive fine characterization techniques that can be used in-situ during processes to optimize them. We believe that this is an area of great potential, where the need for fine-scale simulation tools is once again pressing.
Finally, it would be inconceivable today to imagine the future of predictive tools in metallurgy without considering the notion of massive data and machine learning. We’re obviously fully invested in this area, while retaining what I believe has made our previous tools so successful: developing physically motivated models enriched by the computational power that these methods can bring, for example, in the recognition of complex patterns, the generation of representative microstructures from fragmentary data, the acceleration of calculation times by mixing high-fidelity predictions and reduced-order models, etc. Here again, one of our original features is to have both the experimental and numerical skills to build high-value-added databases to train our models.
Modeling the grain growth mechanism using supervised learning (RealIMotion Chair)
While we often speak of “digital twins” for metallic materials during their elaboration, we are in fact more in the era of the “digital ghost”, where modelling is aimed at understanding and thus optimizing their elaboration paths a posteriori. There is little doubt that the advent of true digital twins, enabling materials to be optimized through real-time process control, will be one of the next revolutions in this field.
Metallic materials will also become increasingly complex. Indeed, in the search for customized properties, we can see the emergence of increasingly “exotic” microstructural characteristics, and therefore potentially new mechanisms to be understood and modeled. The increasing use of recycled materials in the composition of industrial alloys will also be a major issue in the future, in line with current environmental challenges. This is also a major scientific challenge, given the chemical complexity of these new grades, their understanding and certification for strategic applications.
Last but not least, simulations at the microstructure scale inevitably require data to identify the physical parameters of the models used. For certain quantities, it can be very difficult, if not simply impossible, to carry out suitable experimental campaigns to identify them. Coupling with molecular dynamics simulations is now a necessity to improve our descriptions of these parameters at higher scales. This subject is also of prime importance to our team in improving the representativeness of our simulations.
Looking back, I can see that a career can be built on a few inspiring encounters! In fact, I was very lucky to discover CEMEF and the school through two very different points of view, through fascinating and passionate people, and also through a post-doctoral recruitment interview with antagonistic expectations! At the time, Roland Logé and Thierry Coupez were able to convince me that I was the right man for the job on a breakthrough topic that I had absolutely no mastery of, and which in fact didn’t yet really exist in hot forming! A subject at the crossroads between fine metallurgy and numerical front-end tracking methods, where each of us excelled in our own field. It was probably the best (albeit risky!) decision of my career, and I owe them a lot for the total freedom they gave me and the quality of the metallurgical ideas and digital tools/methods they passed on to me. Indeed, what better sandbox for a maths lover than crystallography, the astonishing world of grain boundaries and their thermodynamic or kinetic characteristics, the adaptation of anisotropic finite element meshing and interface capture or tracking approaches for complex networks. If today this is a matter of course (at least for me and, fortunately, for a few colleagues and the students who are now accompanying me on this adventure and to whom I’d like to express my sincere thanks (see photo)), twenty years ago this was absolutely not the case. For this theme to flourish (and for me to do the same), other protagonists were obviously indispensable, first and foremost Yvan Chastel, as head of the MSR team and then director of CEMEF, who was equally attracted by crazy subjects, with boundless energy, and who was willing to take me on one fine morning so that I could continue my wanderings on the same themes at a time when much more down-to-earth research subjects were in the process of taking me away from the Mines Paris – PSL school in 2008.
MSR team photo ( September 2024)
What can I say about Jean-Loup Chenot, illustrious director of CEMEF, who believed in the DIGIMU industrial tool before anyone else, including me! Finally, this adventure could have remained that of a pure numericist if Nathalie Bozzolo hadn’t joined in a little later and made the effort to stick my nose to real materials. What a motivating challenge it was to convince her that most of my simus weren’t just empty shells, like video games to impress the gallery! Thanks to this demand, these subjects took on a new dimension, as we once again brought together very different and complementary skills to answer real academic questions, on equally real materials, with no less real industrial expectations. I think that without realizing it, I ended up becoming as passionate about digital metallurgy as I was about physical metallurgy. Through these encounters, and that’s also why I’m talking about them here, this experience has also taught me the importance of scientific leadership in supporting younger people. Indeed, we’d be lying if we said that the work of a teacher-researcher today isn’t perniciously subject to increasingly heavy and time-consuming administrative burdens, which can distract us from what’s most important in our missions, even within a prestigious, multi-secular entity such as our school. It is therefore important to ensure that scientific excellence remains the watchword in our research teams. I, for one, have been incredibly fortunate to work with these elders, and I owe them a great deal in the construction and structuring of the research theme now rewarded by this medal. Thank you for giving me the opportunity, through this question, to thank them.
Finally, the “we” used throughout this exchange also illustrates for me an obviousness that remains worth recalling. This theme is first and foremost the fruit of a collective effort by a research team, in which each colleague – engineers, technicians, researchers, PhD students and post-docs – has contributed his or her expertise and commitment. Each study, each individual contribution, makes it possible to build a coherent and enriching whole. I’m very grateful to them all.
Henry Proudhon, a researcher at the Centre des Matériaux (CMAT) at Mines Paris – PSL, will be honored with the David Embury 2024 award from the Sociét...