Interview de Marc Bernacki, lauréat de la médaille Albert Portevin 2024 : une reconnaissance pour 20 ans de recherche en métallurgie computationnelle
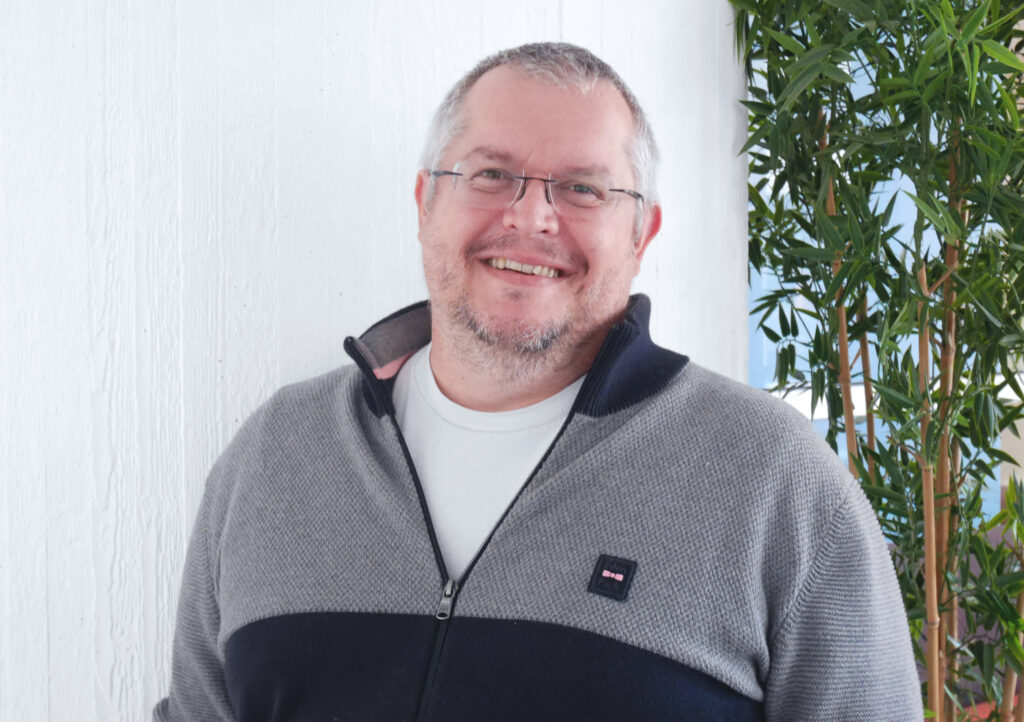
Le 18 novembre 2024, Marc Bernacki sera honoré de la médaille Albert Portevin, une récompense qui célèbre ses contributions en métallurgie physique et computationnelle. Ce prix, décerné par la Société Française de Métallurgie et de Matériaux (SF2M), vient couronner vingt ans de recherches novatrices dans le domaine du calcul haute performance appliqué aux matériaux métalliques.
Marc Bernacki, professeur à Mines Paris – PSL et responsable de l’équipe MSR au CEMEF, contribue par sa recherche au développement de méthodes numériques multi-échelles permettant de décrire et de prédire les transformations microstructurales complexes qui surviennent lors des procédés de mise en forme des métaux. Ses travaux s’inscrivent dans la lignée d’Albert Portevin (1880-1962), dont les recherches sur les matériaux métalliques continuent d’avoir un impact majeur sur les secteurs stratégiques tels que l’aérospatial, la défense, l’énergie et le transport.
Présentation de Marc Bernacki à la remise de la médaille Albert Portevin 2024 le 18 novembre.
Au cours des 20 dernières années, Marc Bernacki a su conjuguer science fondamentale et applications industrielles. En créant des outils numériques originaux pour modéliser des matériaux polycristallins, son équipe a permis une meilleure compréhension des phénomènes microstructuraux tels que la formation de macles, l’évolution des joints de grains ou encore la mobilité des défauts cristallins. Ces sujets sont majeurs pour optimiser les procédés de fabrication métallurgique et les matériaux et prennent pied au travers d’une collaboration constante avec des experts en métallurgie expérimentale. Il est important de rappeler que les enjeux sont de premier ordre d’un point de vue environnemental (meilleur respect des ressources, moins de rebut lors de l’élaboration et optimisation énergétique), sociétale à travers des matériaux plus sûrs et également en termes de souveraineté national pour la conception de matériaux et de procédés plus performants sur des thématiques à fort enjeux tels que dans le domaine de l’énergie, de l’aéronautique ou du spatial.
Reconstruction numérique d’une microstructure polycristalline d’un alliage aéronautique (Inconel718) avec description exacte des particules de seconde phase et statistique des joints de grains.
Les deux chaires ANR industrielles que Marc a obtenues ainsi que son pilotage du consortium Digimu illustrent son dynamisme et son rôle de trait d’union entre recherche fondamentale et applications concrètes. Les simulations développées sont également aujourd’hui appliquées à des domaines émergents comme la métallurgie des poudres, le contrôle non destructif, ou encore la recherche sur des matériaux géologiques et extra-terrestres.
Photo du consortium DIGIMU 2024 à Framatome – Chaire RealMotion.
Photo de plusieurs doctorants et permanents du consortium DIGIMU à SafranTech en 2018.
Au-delà de ses contributions académiques, Marc attache une grande importance à la transmission de son savoir. Il a formé plusieurs générations de jeunes chercheurs à travers l’encadrement de thèses, de post-doctorats et par son enseignement à Mines Paris – PSL. Son engagement dans les partenariats avec l’industrie montre également sa volonté de répondre aux besoins concrets des grands secteurs industriels. À l’occasion de la remise de la médaille Albert Portevin, Marc Bernacki revient sur son parcours et partage ses réflexions sur les perspectives de la métallurgie computationnelle et sur son parcours personnel au sein de l’École.
La métallurgie physique à l’œuvre en mise en forme à chaud est un sujet d’étude depuis 120 ans et dont les grandes théories ayant menées aux premiers modèles phénoménologiques (encore souvent utilisés aujourd’hui dans le monde académique et industriel) datent du milieu du vingtième siècle. Néanmoins, on se rend compte aujourd’hui que la métallurgie physique et expérimentale restent des sciences bien vivantes en termes de recherche académique car beaucoup de phénomènes/mécanismes restent encore incompris voir sont découverts en lien avec des compositions et des modes d’élaboration de plus en plus complexes. Ainsi, il y a encore une vingtaine d’année, il n’existait pas d’outils de simulations réellement prédictif concernant l’évolution des matériaux polycristallins métalliques lors de leur élaboration, ce qui constitue pourtant un besoin crucial de cette thématique. Si certains développements numériques ont été ardus dans leur élaboration et dans la minimisation de leur coût numérique, la tâche la plus difficile à probablement toujours été de se confronter à la réalité de vrais gammes, matériaux et questions industrielles.
Modélisation en grande déformation d’un matériau polycristallin (acier austénitique, nuance pour le nucléaire) avec calculs en plasticité cristalline pour la prédiction des orientations cristallographiques et des densités de dislocations.
En effet, notre équipe interagit avec beaucoup d’équipes étrangères du meilleur niveau sur les simulations dites académiques, c’est-à-dire là ou il s’agit de valider nos outils de simulations sur des conditions idéales, et des matériaux qui le sont tout autant, pour prédire certains mécanismes particuliers à l’équilibre. Dans ce domaine nous avons développé différentes méthodes numériques originales qui nous permettent de proposer des approches différenciantes et génériques. Cependant notre principale réussite réside probablement dans le fait d’être allé au-delà du matériau pur et des conditions idéales. En effet, la réalité des procédés industrielles est tout autre, les mécanismes sont multiples, les microstructures toujours hors équilibre, les matériaux d’une complexité sans nom et c’est sur ce domaine que nous avons réussi des percées majeures en aidant à la compréhension de certains mécanismes, et en permettant l’optimisation de gammes industrielles. Très peu d’équipes osent s’aventurer sur ces sujets. Par ailleurs ce sont ces réussites qui permettent de répondre aux enjeux environnementaux, sociétaux et de souveraineté majeurs détaillés précédemment.
Thématique de recherche générale de l’équipe MSR.
SI d’un point de vue académique, il est assez simple de répondre à cette question au travers des publications et des méthodes qui sont ensuite réutilisées et améliorées dans la communauté ; d’un point de vue industriel il peut être bien plus difficile de répondre d’une manière aussi précise. En effet ou s’arrête le succès d’une méthode numérique réellement prédictive et validée avec nos partenaires industriels commence souvent la confidentialité industrielle des réussites qui peuvent en découler sur le terrain. Il n’en reste pas moins une vraie satisfaction lorsque nous savons, à demi-mot, que telle ou telle simulation a pu permettre de diminuer nettement le taux de rebut sur la fabrication d’une pièce ou lorsque des brevets d’inventions élaborés sur base de campagnes d’essais numériques réalisées avec nos outils, peuvent être déposer pour éviter l’apparition de défauts critiques sur des pièces stratégiques.
La trame de fond à laquelle nous veillons dans l’équipe a toujours été la compréhension physique et expérimentale des phénomènes que nous cherchons à modéliser. C’est difficile mais cela nous permet d’avoir un regard générique sur les mécanismes physiques à l’œuvre et de savoir appliquer notre savoir-faire sur des matériaux différents. Par exemple certains mécanismes à l’œuvre pour les matériaux polycristallins métalliques, afin d’en prédire leurs propriétés mécaniques, peuvent être étendus, avec une autre échelle de temps et d’espace, aux roches pour exhiber des hypothèses sur leur histoire géologique. En poussant à son extrême l’analogie entre caractéristique fine des microstructures résultantes et histoire/ évènements « thermomécaniques » potentiels sous-jacents, nous avons également la chance de pouvoir collaborer à des projets s’intéressant à des matériaux extraterrestres issus d’astéroïdes avec certains collègues de l’observatoire de la Côte d’Azur, de l’université de d’Arizona et de la NASA.
Représentation numérique d’un régolithe d’astéroïde afin d’en modéliser la réponse thermique à l’ensoleillement
Ce côté générique sur les mécanismes et les méthodes numériques nous permet en effet également d’être très agile sur les nouveaux procédés. Nous avons ainsi différents développements dédiés à la métallurgie des poudres et la fabrication additive pour lesquels les besoins en jumeaux numériques sont prégnants.
Représentation numérique d’un agrégat polydisperse dense de particules de poudre avec application en métallurgie des poudres
L’amélioration des techniques de contrôle non destructifs tout comme leur modélisation au sein des matériaux hétérogènes laissent aussi entrevoir dans le futur des techniques de caractérisation fines des matériaux non destructives et utilisable in-situ durant les procédés afin de les optimiser. Nous croyons à cette thématique à très fort potentiel ou là encore le besoin d’outils de simulations aux échelles fines est criant.
Enfin il ne serait pas envisageable aujourd’hui d’imaginer l’avenir d’outils prédictifs en métallurgie sans penser à la notion de données massives et d’apprentissage automatique. Nous sommes évidemment totalement investis sur le sujet tout en conservant ce qui a fait, selon moi, le succès de nos précédents outils: développer des modèles physiquement motivés enrichis par la puissance computationnelle que peuvent par exemple apporter ces méthodes dans la reconnaissance de schémas complexes, la génération de microstructures représentatives à partir de données parcellaires, l’accélération des temps de calculs en mixant prédictions hautes-fidélités et modèles d’ordre réduit,… Là encore une de nos originalités est de disposer à la fois des compétences expérimentales et numériques pour construire des bases de données à hautes valeurs ajoutées pour entrainer nos modèles.
Modélisation du mécanisme de croissance de grain par apprentissage supervisé (chaire RealIMotion)
Si nous parlons aujourd’hui souvent de jumeaux numériques (« digital twin ») pour les matériaux métalliques lors de leur élaboration, nous sommes en fait aujourd’hui plus à l’ère du fantôme numérique (« digital ghost ») où les modélisations visent à comprendre et donc à optimiser à posteriori leurs voies d’élaborations. Il fait peu de doute que l’avènement de vrais jumeaux numériques permettant d’optimiser l’élaboration des matériaux par un contrôle en temps réel des procédés constitue une des prochaines révolutions du domaine.
Les matériaux métalliques seront par ailleurs de plus en plus complexes. En effet, dans la recherche de propriétés à façon, on voit se dessiner la recherche de caractéristiques microstructurales d’un « exotisme » croissant et donc potentiellement de nouveaux mécanismes à comprendre et à modéliser. L’utilisation croissante de matériaux recyclés dans la composition des alliages industriels sera aussi à l’avenir une thématique de première importance en phase avec les enjeux environnementaux actuels. Cela constitue également un enjeu scientifique majeur par la complexité chimique de ces nouvelles nuances, leur compréhension et leur certification sur des applications stratégiques.
Enfin les simulations à l’échelle de la microstructure se nourrissent forcément de données pour identifier les paramètres physiques des modèles utilisées. Sur certaines grandeurs, il peut être aujourd’hui très difficile voire tout simplement impossible de mener des campagnes expérimentales adaptées pour les identifier. Le couplage à des simulations en dynamique moléculaire est aujourd’hui une nécessité pour améliorer nos descriptions de ces paramètres aux échelles supérieures. Ce sujet est également de première importance pour notre équipe dans l’amélioration de la représentativité de nos simulations.
En regardant en arrière, je me dis qu’une carrière tient parfois à quelques rencontres inspirantes ! J’ai en effet eu beaucoup de chance de découvrir le CEMEF et l’école au travers de deux regards très différents, de gens passionnants et passionnés et aussi d’un entretien de recrutement en postdoctorat avec des attentes antagonistes ! En effet à l’époque Roland Logé et Thierry Coupez ont su me convaincre que j’étais l’homme de la situation sur une thématique en rupture de l’état de l’art que je ne maitrisais absolument pas et qui en fait n’existait pas encore vraiment en mise en forme à chaud ! Un sujet à la croisée entre métallurgie fine et méthodes numériques de suivi de front où chacun des deux excellait dans son propre domaine. Il s’agira probablement de la meilleure (bien que risquée !) décision de ma carrière, je leur dois beaucoup par la liberté totale qu’ils m’ont laissée et la qualité des idées en métallurgie et des outils/méthodes numériques qu’ils m’ont transmis. En effet, quel meilleur bac à sable pour un amoureux des maths que la cristallographie, le monde étonnant des joints de grains, et de leurs caractéristiques thermodynamiques ou cinétiques, l’adaptation de maillage éléments finis anisotropes et les approches de type capture ou suivi d’interfaces pour des réseaux complexes. Si aujourd’hui cela coule de source (au moins pour moi et, heureusement, pour quelques collègues et les étudiants qui m’accompagnent maintenant dans l’aventure et que je remercie grandement, cf photo !), il y a vingt ans ce n’était absolument pas le cas. Pour que cette thématique puisse s’épanouir (et moi de même), d’autres protagonistes ont évidemment été indispensables, Yvan Chastel tout d’abord, en tant que responsable de l’équipe MSR puis directeur du CEMEF, tout aussi attiré par les sujets fous, à l’énergie toujours débordante et qui a voulu m’embaucher un beau matin pour que je puisse continuer mes pérégrinations sur les mêmes thématiques alors que des sujets de recherche beaucoup plus terre-à-terre étaient en passe de m’éloigner de l’école de Mines Paris – PSL en 2008.
Photo d’équipe MSR (septembre 2024)
Que dire de Jean-Loup Chenot, illustre directeur du CEMEF qui a cru à l’outil industriel DIGIMU avant tout le monde, moi y compris ! Enfin, cette aventure aurait pu rester celle d’un pur numéricien si Nathalie Bozzolo n’avait pas rejoint l’aventure un peu plus tard et n’avait pas fait l’effort de me coller le nez sur de vrais matériaux. Quel challenge motivant que d‘arriver à la convaincre que la plupart de mes simus n’étaient alors pas qu’une coquille vide, du genre jeu vidéo pour épater la galerie ! Grâce à cette exigence, ces sujets ont pris une nouvelle dimension en croisant à nouveau entre nous des compétences très différentes et complémentaires pour répondre à des questions académiques réelles, sur des matériaux tout aussi réels, avec des attentes industrielles non moins réelles. Je crois que sans m’en rendre compte, j’ai bien fini par devenir, grâce à cela, aussi passionné par la métallurgie numérique que la métallurgie physique. A travers ces rencontres, et c’est aussi pour cela que j’en parle ici, cette expérience m’a aussi enseigné l’importance du leadership scientifique pour accompagner les plus jeunes. En effet, nous nous mentirions de dire que le travail d’enseignant chercheur n’est pas aujourd’hui soumis, de manière pernicieuse, à des charges administratives de plus en plus lourdes et chronophages qui peuvent nous éloigner du plus important dans nos missions même au sein d’une entité prestigieuse multiséculaire comme notre école. Il est donc important de veiller à ce que l’exemple par l’excellence scientifique reste le maître mot dans nos équipes de recherche. J’ai, je crois, pour ma part, eu cette chance incroyable avec ces ainés et je leur dois beaucoup dans la construction et la structuration de cette thématique de recherche aujourd’hui récompensée par cette médaille. Merci de m’avoir donné, à travers cette question, la chance, ici, de les en remercier.
Enfin, le « nous » utilisé tout au long de cet échange illustre également pour moi une évidence qu’il reste bon de rappeler. Cette thématique est avant tout le fruit d’un effort collectif d’une équipe de recherche, où chaque collègue – ingénieurs, techniciens, chercheurs, doctorants, et post-doctorants – a apporté sa pierre à l’édifice, son expertise et son engagement. Chaque étude, chaque contribution individuelle, permet de construire un ensemble cohérent et enrichissant. Je leur en suis très reconnaissant.
Henry Proudhon, chercheur au Centre des Matériaux (CMAT) de Mines Paris – PSL, sera honoré par le prix David Embury 2024 de la Société Française de Mé...